Welded wire panels, a staple in construction and agriculture, have continuously evolved to accommodate a myriad of applications. Their versatility and robustness make them an ideal choice for various industries, and their understanding can significantly enhance both safety and efficiency in projects.
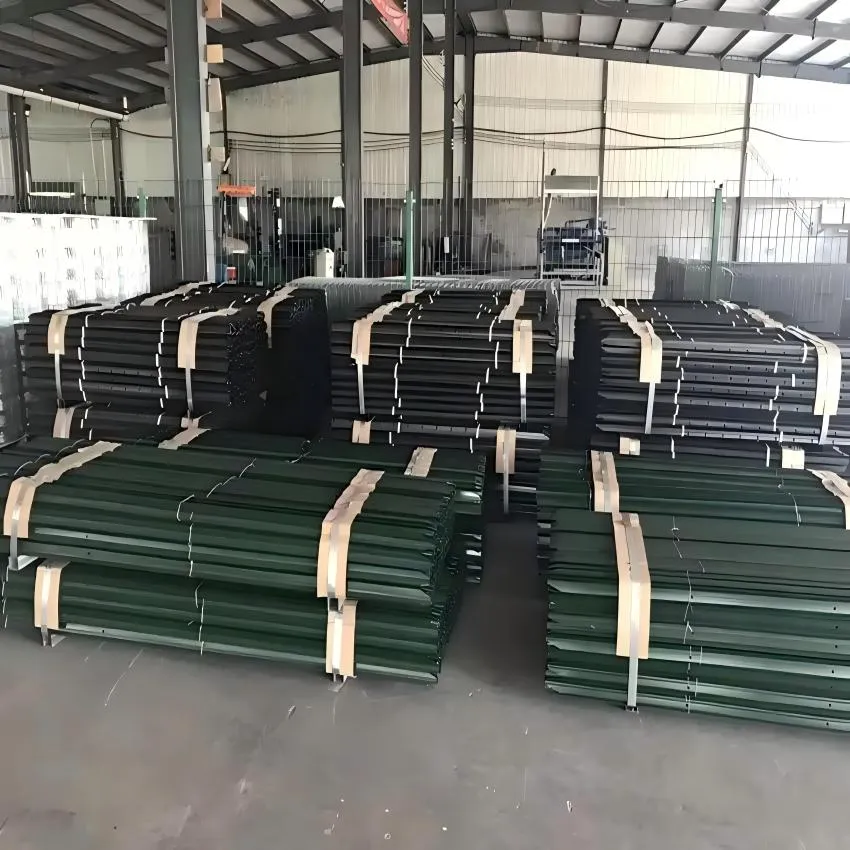
Experience in using welded wire panels often begins with recognizing their inherent advantages. For instance, many seasoned contractors appreciate that these panels come pre-welded in a grid, ensuring uniformity and eliminating guesswork on the site. This efficiency not only saves time but also optimizes labor costs, particularly for large-scale projects. Finishing tasks swiftly without compromising quality can be the difference between landing the next contract or losing it to a competitor.
From an expertise standpoint, knowing the specifics of welded wire panels can be a game-changer. These panels are composed of high-quality steel, undergo rigorous welding processes, and are subsequently galvanized for corrosion resistance. Such specific designs cater to critical demands in areas prone to harsh environmental elements. For example, in saline environments or areas with high humidity, a galvanized welded panel resists degradation, ensuring structural integrity far beyond that of non-treated alternatives.
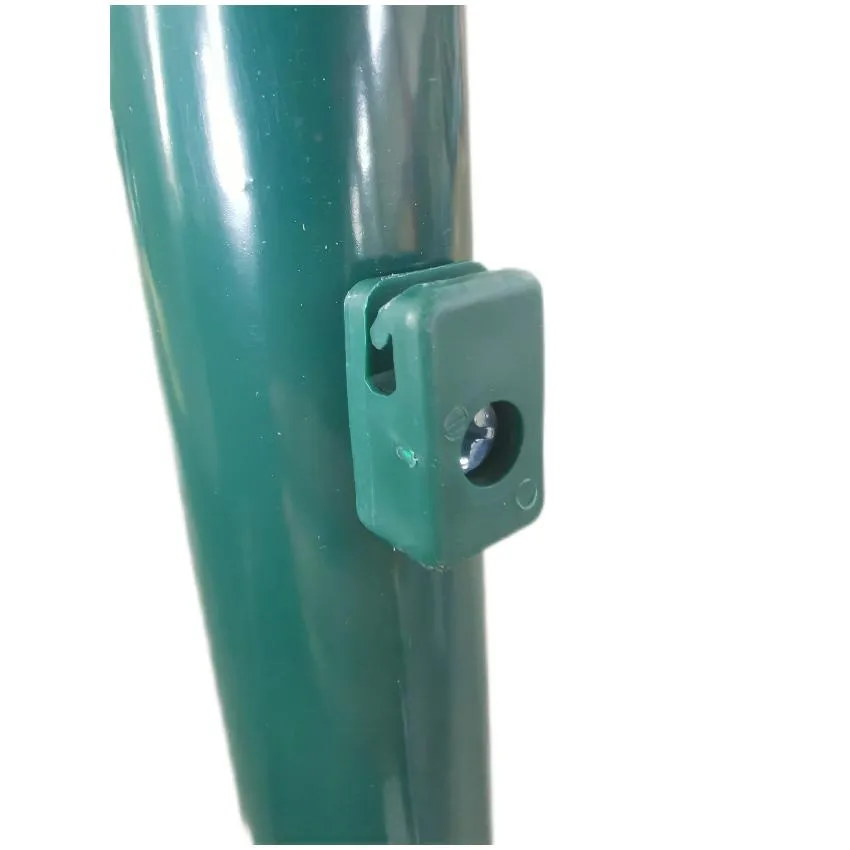
When selecting welded wire panels, considering the load-bearing capacity is essential. Experts often recommend heavier gauge wire for projects that require substantial support, such as retaining walls or industrial fencing. Conversely, for applications like garden enclosures or poultry pens, lighter gauge wire often suffices, balancing cost and function effectively. Understanding these nuances distinguishes professionals in the field and enhances project outcomes.
welded wire panels
Authority in the welded wire panel market is often built through years of innovation and service excellence. Leading manufacturers, who have set industry standards, continuously strive to improve panel design, addressing both safety and functionality. By staying updated with these advancements, companies can enhance their offerings and maintain a competitive edge. Moreover, adopting quality certifications and adhering to international standards amplifies a company's authority, assuring clients of product reliability.
Trustworthiness, an indispensable facet in construction, is equally significant when dealing with welded wire panels. Selecting a supplier with a proven track record reassures clients of product longevity and performance. Testimonials and case studies frequently serve as powerful testimonials to potential clients, demonstrating a company's capability to deliver under diverse conditions. A transparent approach, clear communication, and prompt after-sales service solidify a supplier's reliability, cultivating long-term client relationships.
An understanding of these panels also extends to their environmental impact. As more emphasis is placed on sustainable construction practices, welded wire panels offer an eco-friendly alternative. Their production process requires less energy compared to materials like wood or concrete. Additionally, their recyclability adds to their green appeal, aligning with global efforts to minimize ecological footprints.
In the ever-evolving landscape of construction and agriculture, welded wire panels present a reliable and versatile solution. When paired with expertise, authority, and trustworthiness, these panels can transform projects, yielding outcomes that stand the test of time and nature. By leveraging the collective experiences of industry veterans and the innovative strides taken by leading manufacturers, professionals can harness the full potential of welded wire panels, ensuring both safety and efficiency are paramount.